Thermal product treatment for the best beer quality
Natural, tasty and durable
Procedures for the product preservation and safe, hygienic sequences are essential factors when it comes to product manufacture – and this obviously also applies to beer. The Krones VarioFlash B flash pasteuriser guarantees the safe microbiological filling of beer. Since every product has its own requirements, Krones adjusts the machine individually to suit the respective applications.
At a glance:
- Output range from 1,800 to 60,000 litres per hour
- Fields of application: beer, flavoured beer, wine and spritzers
- Enhanced beer quality with express pasteurisation
- If the line is stopped: "Eco-hygienic sleep mode" stand-by operation for minimal energy and water consumption
- Highest microbiological safety thanks to line sterilisation and variable PU control
- Intelligent use of surplus energy, such as from the bottle washer
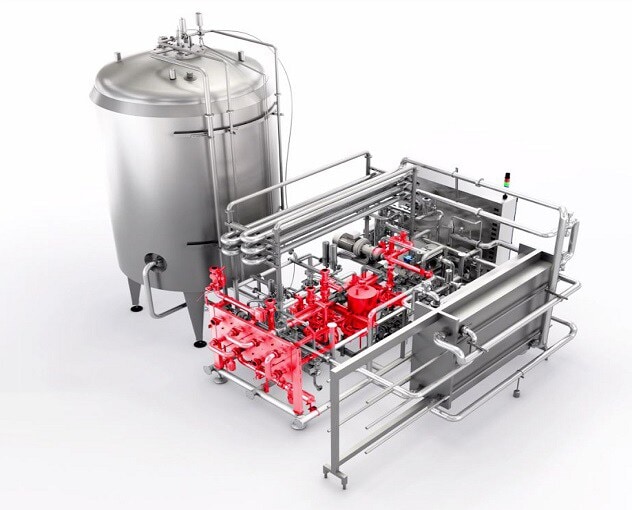
Direct connection or via swing bend panel or valve manifold
- Quality control possible during product change-overs
- Possible integration of a venting lantern to discharge the released CO₂
Direct connection or via swing bend panel or valve manifold
- Quality control possible during product change-overs
- Possible integration of a venting lantern to discharge the released CO₂
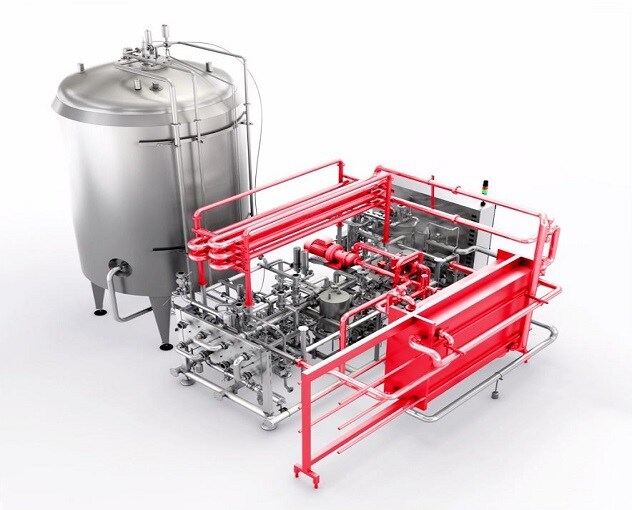
Hygienic plate heat exchanger constructed in accordance with Krones specifications
- For gentle and reliable product heating
- Heat retention with redundant temperature control
Hygienic plate heat exchanger constructed in accordance with Krones specifications
- For gentle and reliable product heating
- Heat retention with redundant temperature control
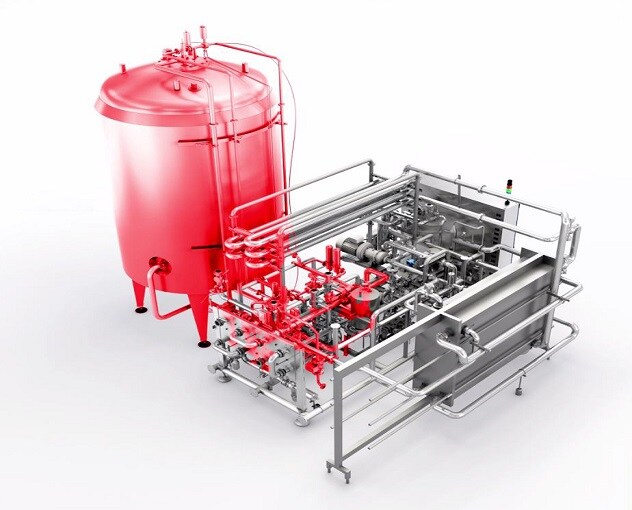
- Decouples the heating process from the filler
- Balances out production fluctuations
- Ensures an unvarying and consistent supply of the product to the filler
- Decouples the heating process from the filler
- Balances out production fluctuations
- Ensures an unvarying and consistent supply of the product to the filler
Optional additional module: Integrated carbonation
Krones is the only manufacturer on the market to integrate a module for carbonation directly in the heating system.
Benefits to you
- Considerably smaller footprint (than if it were to be installed as an individual machine): no additional buffer tank needed as the existing product tank acts as a buffer
- Everything in a single system: Sanitisation is possible directly through the hot-water circuit in the VarioFlash B
- Optimal microbiological conditions: omission of unnecessary components after product heating
- Highest CO₂ dosing accuracy: ≦ 0.08 g/l (temperature-dependent, if production conditions remain consistent, described as sigma 1)
- More flexible line concepts possible: e. g. use of a less expensive free-flow plate heat exchanger (compared to the tubular heat exchanger)
- Many years of experience: more than 1,500* delivered Contiflow systems, allowing us to become familiar with the exact challenges presented by carbonation
* As of: June 2022
Benefits to you
High accuracy and product safety
The high-precision PU control provides guaranteed microbiological quality by using the maximum buffer capacity. The exact adherence of the selected heating temperature is redundantly monitored.
Flexibility in the production process
Product changes can be realised within just 30 minutes (between the last and the first bottle) with intermediate water rinsing and appropriate hardware and software.
Hundreds of satisfied customers
The VarioFlash is a model for success: With more than 250* reference customers, this system is one of our most-built units, guaranteeing best product quality worldwide.
Hygienic design
The compact and hygienic design ensures high process safety, eases maintenance and reduces the loss of product through reduced mixing phases during the start and stop phases.
Precise tracking of all operation steps
All process-relevant parameters are saved and archived by an electronic data writer.
Hygienic design
The compact and hygienic design ensures high process safety, eases maintenance and reduces the loss of product through reduced mixing phases during the start and stop phases.
Economic efficiency and best product quality
Our systems for energy recovery and the patented standby mode reduce the consumption of energy. Innovative procedures like the express pasteurisation provide improved beer quality on top.
* As of: June 2022
This is why the VarioFlash B is enviro-classified:
Energy efficiency
- Patented "Eco-hygienic Sleep Mode" stand-by operation for minimal energy and water consumption
- Heat regeneration through the bottle washer
- Heat exchanger designed for the product of each customer
- Internal heat recovery of up to 95 percent
Media efficiency
- Intelligent buffer tank control reduces the consumption of CO₂