Brewing technology for the fermentative production of alternative proteins
Using precision fermentation, animal or plant cells can be specifically programmed or optimised to produce a specific product such as enzymes, fats, proteins, vitamins, flavourings and natural pigments. Fermentatively produced proteins can then be combined with other ingredients and further processed to reproduce meat, egg or dairy products.
A concrete example of the cultivation and replication of such proteins is biomass production. Here, cells are placed in a tank where cell multiplication is initiated. And this is exactly where Steinecker comes into play with its own bioreactor. The key factor: It was developed on the basis of the proven Poseidon fermentation unit from brewing technology and works with a circulation unit instead of an agitator. In addition, the recirculation unit is equipped with aseptic valve technology from Evoguard and a low-shear aseptic pump. Integrated in a sterile tank with steam or condensate barrier, cells can be cultivated or fermentations carried out.
Tasks of a bioreactor
Homogenization |
|
Mixing |
|
Aeration |
|
Feeding |
|
Sampling | |
Sterile environment |
|
The recirculation of the tank volume under sterile conditions is the key task of an efficient fermentation process.
Method of operation of the dynamic fermentation
Recirculation for an efficient fermentation
Flexibility and scalability
- Available tank sizes: between 500 and 100,000 litres
- Prototype on a laboratory scale, validation and test capacities possible with partners
- Various outlet housings at different heights within the tank: are not only used as outlet but also as inlet
- Different flow directions possible (for homogenization, aeration, fluidized bed process or sedimentation for cell harvesting)
- Flexibility through pipe diameter dimensioning and adjustment of the volume flows in the pipe system
- Fed-batch or continuous mode possible
Cost and process efficiency
- Continuous mixing in a recirculation circuit: use of a recirculation unit instead of an agitator
- Can be retrofitted into existing tanks
- Maintainability through easy accessibility of seals, field devices and motors
- Fewer spray shadows during cleaning for an improved cleaning result
- Representative measurement of process parameters by means of continuous flow through the field devices in the circuit
The processes in the bioreactor in detail
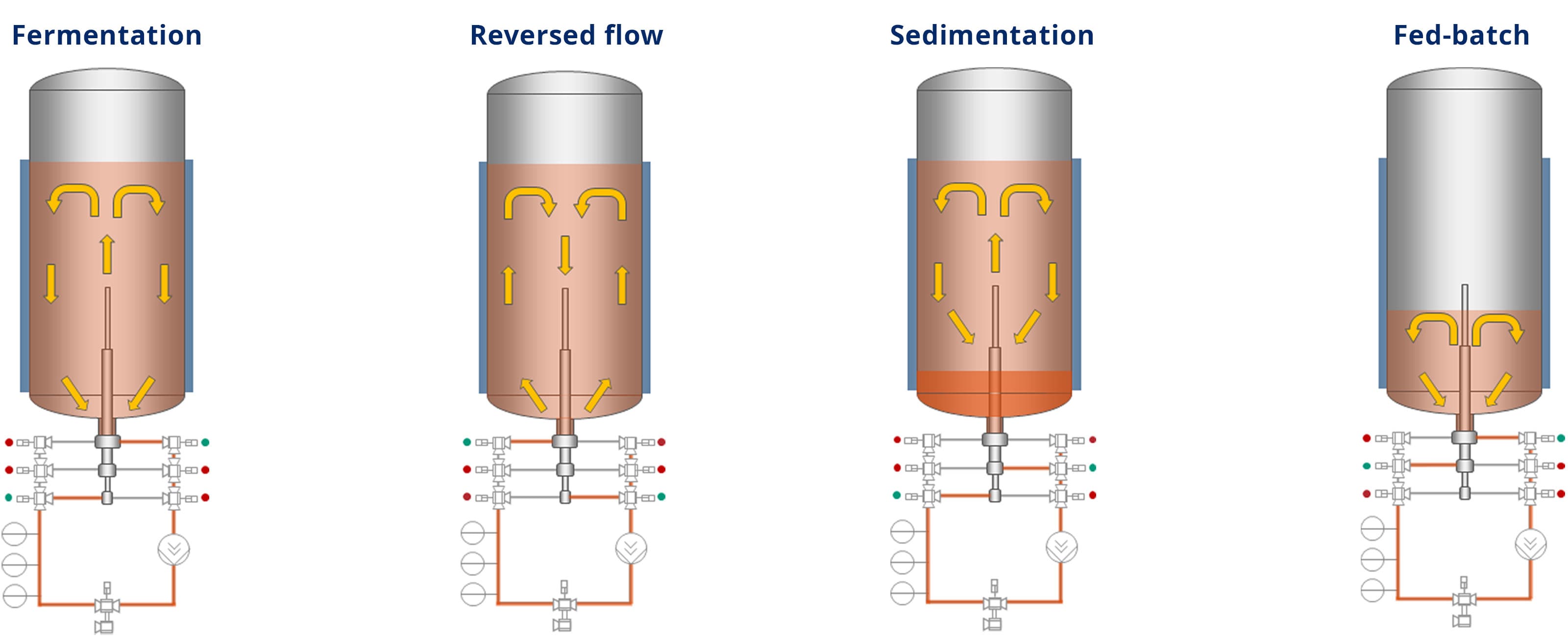
Tank construction – From tank to bioreactor
Our expertise
- Manufacturing halls specially designed for tank construction
- Automated processes for tank dome and shell production
- Precisely coordinated work steps, carried out by qualified welders
- High-performance and program-controlled production machines for cutting, drawing and welding work
- Highest quality through a globally recognised and standardised welding and inspection procedure
- Surface treatment with polishing and pickling solutions, including ceramic blasting of the outer surfaces
The benefits of the Steinecker bioreactor
Efficient solution for high production outputs
The use of a recirculation unit enables the realisation of high production volumes, and the costs still remain within reasonable limits.
Use of approved technology
As the bioreactor is based on the concept of the Steinecker Poseidon, it is based on a tried-and-tested technology that has already proved successful in practice at numerous breweries.
Many years of experience in plant engineering
As expert in brewing technology, Steinecker can look back on almost 150 years of experience in plant engineering. Customers who want to open up completely new markets in the field of fermentative production of alternative proteins are now also benefiting from this knowledge and are utilising Steinecker's proven technology to do so.